Category Archive: Teflon Coatings
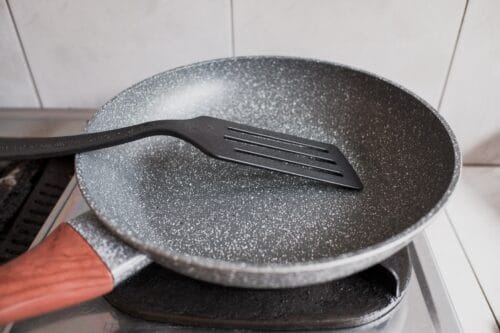
Nonstick surfaces are the unsung heroes of the food and beverage industry. They are truly a modern marvel that we all take for granted. They are relied on for many reasons, including efficiency, cleanliness, maintaining high production standards, and safety. Nonstick coatings are one of the world’s innovative technologies that also reduce waste, improve food safety, and go along with FDA standards. The bottom line is that nonstick surfaces are essential in your food and beverage operation.
Step Back In Teflon Time: A Nonstick History
Nonstick technology dates back to the 20th century and like many innovations, was an accident. A scientist who was experimenting with refrigerants discovered the gas he was using solidified into a slippery surface. Later, called Teflon, this invention was the beginning of modern nonstick cookware. Although not available to everyone until the 1950s, it quickly became a household staple. Throughout the years, it continued to grow and evolve and was used for a variety of applications. Today, nonstick is essential in homes and industries. The expert and knowledgeable Sun Coating Company team has an array of coatings that are the ideal solution for your industry, product, and application.
Take a look at why nonstick coatings are game changers:
Enhances Equipment Performance and Extends Equipment Life
Nonstick coatings, like Chemours Teflon finish, create a slick surface that prevents food from sticking to machinery and cookware. Chemours Teflon®’s industrial coating can be used on multiple services including carbon steel, aluminum, stainless steel, steel alloys, brass, and magnesium. Additionally, it can be used on non-metallics such as glass, fiberglass, some rubber, and plastics. No excessive oils or lubricants are needed, resulting in a healthier food product and a streamlined cooking process. It also extends the life of the equipment.
Reduces Waste and Provides Cost Savings
One of the biggest challenges in the food and beverage industry is product loss from ingredients sticking to everything from pots and pans to conveyor belts. Nonstick coatings prevent this issue; fewer products are wasted. For example, the baking industry benefits greatly, especially when sticky ingredients like caramel and dough are commonly used.
Improves Cleaning and Maintenance
Nonstick coatings make cleaning faster, easier, and more efficient. Since the food doesn’t stick to the coated surfaces, it is easier and quicker to clean. Additionally, less water and cleaning solutions are needed adding to cost savings and environmental benefits.
Ensures FDA Compliance and Food Safety
The food and beverage industry is faced with complying with strict safety regulations. Many FDA compliance coatings are used to meet these non-negotiable food safety requirements. Nonstick coatings withstand high temperatures, resist chemical interactions, and prevent contamination. They are ideal for beverage filling machines, storage tanks, processing equipment, and food-grade containers and packaging. You’ll find nonstick applications on baking trays, frying pans, ice cream scoops, conveyor belts, and mixing equipment.
Contact Sun Coating Company Today
Nonstick coatings like Chemours Teflon finish are FDA compliance coatings that are instrumental to helping businesses maintain high standards that are expected in our modern-day operations. Many companies recognize that overcoming “sticking” is a way to improve their operations and, more importantly, their profitability. To compete in a global economy, most areas of manufacturing and industrial processing must find ways to make their products better, faster, and safer, while lowering costs of production. We have the answer…FDA-approved and customer-approved nonstick coatings. We have helped hundreds of satisfied customers and can help you, too. Sun Coating Company has sixty years of experience applying Chemours Teflon coatings and others that will improve your production process. Our knowledgeable, expert, and trained team can show you how to improve your operations. Contact us today.
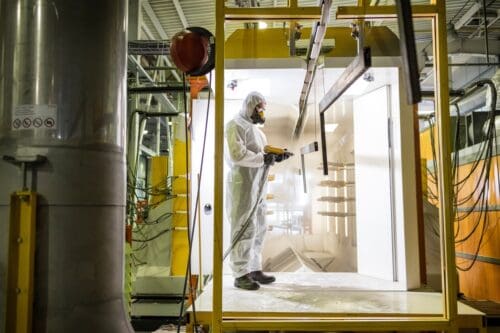
Equipment needs to run smoothly in engineering applications, and that means you need to do whatever you can to reduce friction. Low-friction coatings are a very good option because they last a long time, reduce the need for maintenance, and help your equipment function more smoothly in general. Low-friction coatings have secondary benefits, as well.
Why Use a Coating Instead of a Lubricant?
If you’ve got two parts that touch during equipment operation, why not just use a plain, cheap lubricant like grease or oil? Why go through the expense of coating the parts?
Sometimes, it’s just not practical to use a liquid lubricant. Maybe you can’t have liquid or greasy substances on the parts, or there’s no way to contain the liquid so that it doesn’t drip onto other parts of the equipment. For whatever reason, using a permanent, dry coating would be better in these cases. Other times, the maintenance needed to replenish the liquid lubricant may be something you don’t want to deal with. In that case, too, a dry coating would be more helpful.
It’s also possible to use both a liquid/grease lubricant and a low-friction coating. That coating acts as a backup just in case something goes wrong with the liquid lubricant, such as a leak that lets it drain away.
Why Is Friction so Undesirable?
Severe friction is obviously a problem, but is a little friction really that bad? Yes, even a little friction can lead to premature wear on parts. That increases your repair costs and takes up more of your time. Friction can also lead to excess heat generation that can damage parts and make the working environment uncomfortable for anyone who has to be near the equipment.
Friction — even a little bit — can lead to more drag on the parts. It makes it more difficult for the parts to move smoothly and increases the energy needed to force the parts through. It may not look like it to you as you watch the equipment work, but the engine can feel it. And that extra effort needed can build up over time and wear down the engine prematurely. That little bit of friction can set off a chain reaction that leads to parts needing more frequent maintenance and replacement.
Can Low-Friction Coatings Protect Against Corrosion?
As long as the coating remains intact, it can protect the surface it’s on from corrosion. This is why you need to apply a high-quality coating that’s appropriate for the particular environment and equipment. You want something that’s durable enough to withstand any contact with other parts of the equipment (e.g., gear trains) and that can withstand environmental conditions.
Is Contamination a Concern?
Any surface can technically be contaminated with different substances, but low-friction coatings release any material that gets stuck to them more easily. If grease or dirt lands on the coating, it should be easier to wipe those away to prevent them from contaminating the rest of the equipment. This is another reason why you want to ensure the low-friction coating you choose is appropriate for the equipment in question. If the equipment is exposed to corrosive liquids, for example, a coating that isn’t resistant to those liquids will only disintegrate and become a contaminant itself.
Low-friction coatings that are also nonstick are terrific for molds, such as polyurethane foam mold coatings, as they’ll release finished parts more easily, too. There’s less of a risk of some of the molded material staying behind when you remove the finished part.
Contact Sun Coating Company if you have equipment that’s in need of low-friction coatings. Whether you need a coating for a structural engineering project or have equipment that needs food processing coating, we have what you’re looking for.
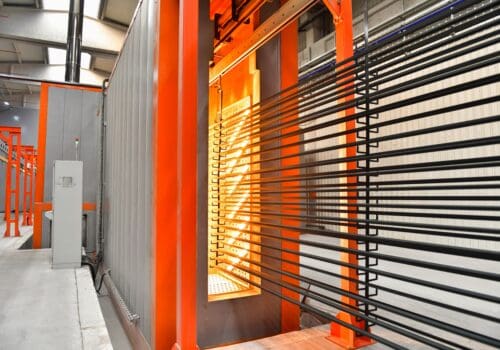
Operating in extreme-temperature environments poses unique challenges for materials and coatings. Whether in frigid arctic conditions or blazing hot furnaces, specialized high-temperature coatings are often required to protect parts and equipment. At Sun Coating Company, we understand the demanding requirements of high-heat applications and offer a range of durable, high-performance coatings to meet your needs.
Withstanding Extreme Temperatures
For components and parts exposed to very high temperatures, choosing the right protective coating is critical. Without proper thermal protection, metals and alloys can experience oxidation, corrosion, and breakdown at elevated temperatures. High-temperature coatings act as a barrier, preventing damage to the underlying substrate.
Coatings for extreme heat applications must maintain their mechanical properties and adhesion at temperature. For instance, a coating that becomes too soft or fluid at high temperatures will drip or peel away, leaving the surface unprotected. Proper formulation is essential. Advanced resins and thermally stable pigments are incorporated so the coating film retains integrity even when red-hot.
At Sun Coating Company, we offer specialty Sandstrom Mil-Spec coatings designed to perform at up to 1000°F. These MIL-SPEC qualified lubricants withstand searing temperatures without burning off or decomposing. The bonded film structure remains intact, protecting critical components like firearms, aerospace parts, engines, and exhaust systems.
Protection Beyond Heat Resistance
While resisting extreme temperatures is the primary function, high-heat coatings offer additional benefits:
- Corrosion resistance – The coating forms a protective barrier inhibiting rust and oxidation at elevated temperatures.
- Wear resistance – Specialized resins and crosslinked structures provide hardness to resist scratching and abrasion.
- Lubricity – Solid lubricants like PTFE or molybdenum disulfide lower friction, preventing galling/wear.
- Chemical resistance – Thermal coatings are highly resistant to oils, fuels, cleaners, and other chemicals.
This combination of properties ensures longevity by protecting against corrosion, friction, chemicals, and abrasive wear – even at extreme temperatures.
Choice of Chemistry
There are a variety of resin chemistries used in high-heat coatings, each with relative advantages:
- Silicone – Withstands up to 600°F. Provides lubricity and release properties.
- Polyamide-Imide – Service up to 700°F. Abrasion resistant.
- Fluoropolymer – Non-stick PTFE types stable to 500°F. Chemically inert.
- Inorganic Ceramic – For very high heat up to 1800°F. Insulating. Hard.
Dry film lubricants like our Sandstrom coatings use specialized PTFE and MoS2 resins to retain lubricity even at 1000°F temperatures.
Understanding application requirements helps guide the selection of the optimal coating chemistry. Factors like operating temperature range, substrate material, corrosion risks, lubrication needs, and abrasion all play a role. Our team can help recommend the best coating solution for your extreme environment.
Application Methods
Proper application of high-temperature coatings is also critical for performance. At Sun Coating Company, we use specialized techniques to ensure a uniform, consistent coating film:
- Spray – High transfer efficiency air spray or airless spray allows for coating intricate parts.
- Dip Spin – Complex geometries are coated by dipping and then spinning off excess.
- Brush – For small repairs or touch-ups, brushing works well.
Prior to coating, surfaces are thoroughly cleaned and often abrasively blasted to promote adhesion. Parts are then coated, allowed to dry, and cured at elevated temperatures to fully crosslink the coating. Strict quality control and testing ensure coatings meet required specifications.
Ready to Learn More? Give Us a Call
With decades of coating expertise, Sun Coating Company understands the unique requirements of high-temperature coatings. Our Sandstrom Mil-Spec Coatings and specialty coatings are formulated to withstand extreme heat up to 1000°F while providing lubricity, corrosion resistance, and abrasion resistance. Strict quality standards and controlled application methods ensure coatings will perform reliably in the harshest environments. Contact our team today to discuss your extreme temperature coating challenges.
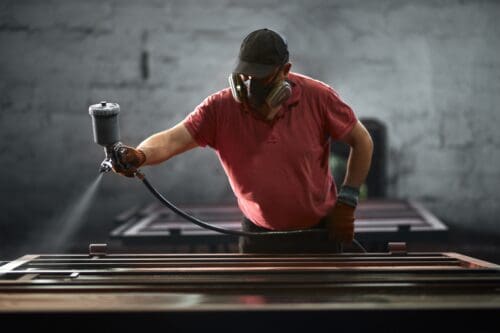
Your industrial machinery is the lifeblood of your business. Without your industrial equipment, you would not be able to engage in your day-to-day operations. As such, a lot of work goes into making sure that your machinery is functioning optimally. But one area that you may not have focused on yet is coatings. Industrial coatings offer numerous benefits for industrial machinery, including extending their lifespan. Here’s how coatings can extend the life of your industrial equipment, why it’s essential to apply coatings, and how you can begin preserving and bolstering your machinery with the support of us here at Sun Coating Company.
The Role of Industrial Coatings in Equipment Life
Industrial coatings are coatings that are applied to a substrate to act as a barrier between the metal and the elements that it may encounter when exposed to the environment bare. At the most basic level, industrial machinery is subject to friction and force, which can gradually wear down the metal and cause external damage over time. But there are other threats in the work environment too. These include caustic chemicals that corrode the metal on your machinery, high temperatures (for which we recommend something like Cerakote coatings), and UV rays that machinery in certain industries may face. Applying industrial coatings to your machinery serves to defend your machinery against these common threats, ensuring that the coatings take gradual damage while your machine components remain protected underneath. While your machinery will still fail over time as it’s expected to, it will be less likely to be due to various components of it failing because of the external factors wearing them down to the point where they’re becoming a hindrance. This keeps your machinery running optimally for as long as physically possible.
Why the Life of Your Machines Is Crucial to Your Business
If you haven’t used coatings in your business before, you might be asking, why now? Why is it essential to pursue this additional service?
Applying coatings to your industrial machinery is crucial for several reasons. The first reason that you’ll want to keep in mind when weighing whether or not to get coatings is the cost of having to regularly maintain or replace machinery. With coatings, your machinery is better protected, meaning that it will function for much longer stretches of time without component failure. But if you don’t have these additional coatings on your machinery, your machinery will likely get run down faster due to corrosion and abrasion. This will require you to replace parts or even replace whole equipment before you should need to. This is costly, and it’s going to have a major impact on your bottom line.
The second reason why coatings are crucial to your business is that they help to reduce downtime associated with machinery repairs. If your industrial machinery begins to degrade rapidly because of environmental conditions, you need to take time out away from production in order to address these repairs. This only becomes more problematic and impactful when you need to replace entire equipment because it has become worn down and non-functional. Productivity is necessary to maintain. With industrial coatings, you can prevent yourself from having to conduct regular repairs so that you can keep the manufacturing process running smoothly and relatively unimpeded. Just take care to select the right coating for your equipment, be it Sandstrom coating or other coating options. Choosing the wrong coating can result in more problems rather than fewer!
Protect Your Industrial Machinery With the Help of Sun Coating Company
Your industrial machinery is only as effective as the care you put into it. Sun Coating Company can help you extend the life of your machinery and bolster your operations with high-performance industrial coatings. Reach out to us today to request a quote!
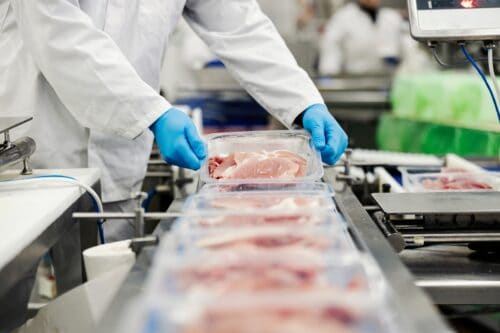
Any item that comes into contact with food or that even sits near food in a processing plant has to be safe for that purpose. That means that any coatings on the equipment and furniture, including noise and squeak reduction coatings, and anything else in the plant must be approved to be in that environment. This is to protect the food and any packaging or other food-adjacent items that pass through. Not using the right coatings can create a major safety problem that affects not only consumers but also your company’s future.
Food Processing vs. Food Packaging and Equipment Manufacturing
Two types of approvals for food-safe items exist. One is the USDA, which handles the processing of actual food, while the other is the FDA, which covers packaging, dishware, utensils, and many other food-adjacent products, such as the processing equipment itself. If it’s going to touch food or be near food but not actually be an ingredient, the FDA likely has oversight.
Prevention of Chemical Leaching and Physical Flaking
Why is the use of FDA-approved coatings so important? If the company making the coating has a great track record, isn’t that better than a company that was FDA-approved but still had problems? No, it’s not because you still don’t know what standards that company’s manufacturing process is trying to meet. An FDA-approved coating has been through stringent evaluation, and you can be reasonably sure that this coating won’t leach chemicals or flake into food, for example. With an FDA-approved coating, you know that the food that will eventually go into that packaging will be as safe from contamination as possible.
Lack of Immediate Effects Doesn’t Mean Lack of Long-Term Effects
One of the issues with getting people to accept that they have to use FDA-approved coatings is that they don’t often see immediate effects from using the wrong product. This is not usually an issue with larger companies, but for smaller operations that are just investigating what they need to set up their business, FDA coatings may seem like one more rule among many. But they’re very important.
A paperboard box holding cookies doesn’t appear to do anything to the cookies, so people assume the box is safe to use with food. However, the lack of immediate effects that you can see right on those cookies does not mean that the person who eats them won’t have long-term effects. If the coating on the inside of the box leaches into the food, you aren’t going to know what it will do for a while. You could find months later that people were ingesting coating chemicals because the lining on the box was faulty, and that’s the sort of stuff that leads to class-action suits. You’re much better off finding FDA-approved coatings for your packaging so that you reduce the risk of something like that leaching.
Compliance With Changing Regulations
One more reason to use FDA-approved coatings is that the companies that make them have to stay aware of any regulatory changes. If the FDA makes a requirement more stringent, the coating manufacturer has to follow those guidelines. There’s no guesswork about whether the polyurethane foam mold coatings you’re using are up to the latest standards. Coatings from companies that try to avoid FDA regulations could be woefully out of date.
At Sun Coating Company, we want your food-adjacent items to be thoroughly safe to use in processing food. Contact us to learn more about different coatings and how to apply them. You want your products to be safe and durable, and ensuring you use an FDA-approved coating is one of the best ways to do that. No matter what you manufacture, if it’s going to be near food, use FDA-approved coatings to keep your customers and consumers overall happy with each product.
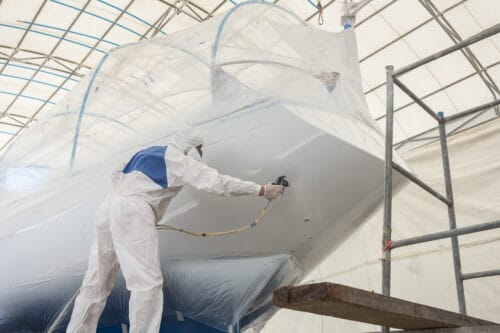
Corrosion isn’t a minor issue for the marine industry; if not addressed properly, corrosion can mean the end of a ship’s sailing days. Salt water can siphon away electrons from metal, leading the metal to essentially weaken, and the water, its oxygen content, and metal can react and create rust. A company sending out a marine vessel or using marine equipment needs to add anti-corrosion coatings to any surface that might potentially be exposed to the humid, salty environment.
Why Is Corrosion Such a Problem for the Marine Industry?
Corrosion can affect even strong metals like steel. Simply having a well-built ship made of durable metal isn’t enough; the water will quickly get to work on the metal and promote corrosion. That can lead to equipment breakdowns and even hull failure. At best, the corrosion simply looks terrible, but it’s also possible that the corrosion could mean a lot of repairs.
It’s Not Just the Water You Need to Worry About
Most people worry about the salty water against the metal surface of the ship, but that’s not the only part of the environment that can cause corrosion on marine vessels and equipment. Salty air itself can also promote corrosion, and that’s even more insidious because you don’t think about the salty air touching metal. You can see water lapping up against the hull and spray from waves hitting equipment, but you don’t have such a visual reminder that air molecules are having an effect, even though they’re constantly in contact with the surfaces that are above water.
The salty, humid air can also affect any cargo and equipment the ship has on board if those aren’t protected. Equipment needs anti-corrosion coatings when possible, and cargo needs to be shielded well from the environment.
Even the Interior Pipes Aren’t Safe
You’re not going to have a perfect vacuum within the walls of the ship, and the humidity and salt in the air will seep their way into every crevice. Unfortunately, this can accelerate the aging and degradation process of pipes (plumbing or otherwise), leading to higher energy usage and more frequent repairs. Neither of these are things you need in general, much less when you’re halfway across the Pacific. Anti-corrosion coatings on plumbing pipes offer direct protection from the effects of humidity and salt, while coatings that have additional insulating properties help protect parts of the ventilation and heating systems. Better pipe integrity leads to better energy savings.
Preventing Corrosion Reduces Maintenance Needs
Any time you can prevent rusting and other corrosion, you’re reducing the need for more maintenance overall. Anti-corrosion coatings don’t eliminate the need for maintenance, obviously, but your tasks should be easier in general, with the need for serious repairs reduced in frequency. And don’t forget that the marine environment can affect the tools and parts you keep around for those repairs, too. Add anti-corrosion coatings to those, too, such as hot plate welding coatings.
You May Have Better Speed and Energy Efficiency
Anti-corrosion coatings offer a couple of extra benefits that you may not have thought about. Some of these coatings help reduce the drag of the water against the hull, and less friction and drag mean less energy is spent fighting currents. The ship’s engines don’t have to work quite as hard to keep an even speed, reducing the strain on the engine and allowing the ship to proceed more smoothly along its path to its next port.
Sun Coating Company offers coatings for most environments, including marine. Contact us to discuss the application and whether you need liquid or powder coatings. If you need a specialty coating, such as Sandstrom Mil-Spec coatings, we offer those, too. Don’t wait to protect the ships and equipment that keep your business running.

The healthcare industry has consistently remained one of the largest in the United States. Projections for 2025 indicate healthcare will continue on an upward trend. One of the important areas in healthcare facilities is food preparation. With many patients on-site, processing food needs to be fast, efficient, and safe. With food processing coatings available from Sun Coating Company, we provide a full line of products.
About Food Processing Coatings
There are many food processing coating options to accommodate the type of coating that best serves your needs. Coatings are available from Chemours Teflon®, reinforced and one-coat finishes from Teflon®, Whitford, Quantum, Excalibur, Xylan®, and more.
At Sun Coating Company, our complete line of food processing coatings is available from Chemours and Whitford. We are a Whitford-recommended coater and a Chemours licensed industrial applicator.
The benefits associated with using FDA-approved food processing coatings have a significant impact on efficiency. Benefits include:
- Easier cleaning.
- Productivity is improved.
- Coatings promote non-sticking surfaces.
- Downtime is significantly reduced.
- Surfaces have low friction.
FDA Compliant Coatings
In the healthcare industry, as in many other types of environments, utilizing products that are in compliance with the FDA is a requirement. At Sun Coating Company, we supply customers with Whitford industrial and consumer coating products. Their FDA approved products are used in many industries and serve specific needs. Several of the Whitford coating products are used in industries involving the food processing industry.
PFA+ Powder
PFA+ is scratch-resistant, decreases surface defects and permeation, and is approved by the FDA, which allows the product to be in contact with food.
QuanTanium
A high-strength coating reinforced by titanium that is used in the Aerospace industry. Due to its durability and strength, the coating has moved into kitchenware.
Quantum
Quantum is designed as a reinforced nonstick coating that provides a high level of scratch resistance to cookware to protect the items against abrasion, as well as other items used to prepare food;
Quantum2
The Quantum2 nonstick coating is created using specific ceramic materials that result in superior adhesion and resistance to abrasion. The coating is used in kitchenware and in industrial food processing.
Xylac
The Xylac coatings are used for cookware and other products associated with cookware. The coatings can sustain high temperatures and have high impact resistance, adhere to metallic surfaces, and are resistant to compounds found in dishwashers and other types of cleansers.
XylanHB
The XylanHB coating is ideal for items with rough surfaces. The thick coating provides benefits in two areas: the coating promotes extended wear to items and enhances the product’s durability.
XylanXLR
XylanXLR is a high-end nonstick fluoropolymer coating developed to be heat resistant, supports dry film release, and is resistant to permeation. With its exceptional heat-resistant capabilities, it increases the reduction of food sticking to items, such as industrial bakeware.
Additional Whitford Coatings
- Dykor coatings provide a high resistance to corrosion.
- Eterna’s fluoropolymer technology enhances release properties.
- Excalibur is a reinforced coating developed to be resistant to wear and abrasion.
- Eclipse is a three-coat nonstick system designed with specific materials to create a coating that is long-lasting.
- Xylar’s thin film coatings have been developed for use in environments that are corrosive, abrasive, and have extreme temperatures.
Contact Our Team
At Sun Coating Company, helping support and promote better efficiency and productivity within the healthcare industry’s food processing areas by providing quality high-end coatings is just one of the things we do. For more information, contact us by phone, send us an email, or fill out our online form to request a quote. Either way, our expert staff is here to help.
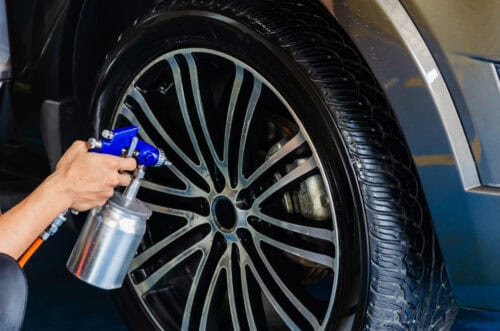
The automotive manufacturing industry continues to be a very important one as it ensures that people have access to the vehicles they need for transportation. As there is a continued demand for new vehicles in the industry today, it is very important that manufacturers are able to keep up. One of the ways that they can do this is by investing in industrial coating services for their heavy equipment and machinery. Industrial coatings play an important role in the overall automotive manufacturing process.
Prevent Corrosion
One of the largest challenges and risks that can come with any type of industrial equipment is corrosion. Rusting can be a very serious issue as it is hard to control once it stops. If it gets bad enough, it can affect the gears and structural support of the equipment. When you invest in a new piece of equipment for your manufacturing process, adding a coating can help you prevent corrosion and rust from occurring, which can help you avoid more serious repair needs.
Proper Lubrication
Any major type of industrial equipment will need to be properly lubricated. When using this equipment, the heavy gears will continue to work, get hot, and work hard. If they are not properly lubricated, this will quickly cause wear and tear. Because of this, investing in dry film lubricant coating can be a great option. When you have this coating placed, it can help keep the equipment lubricated and protected, which can allow you to avoid more significant issues in the future.
Noise and Squeak Management
When it comes to preventing a breakdown of equipment in the auto manufacturing industry, you are likely most concerned with protecting the gears and other parts of the equipment. However, the manufacturing industry also needs to be concerned with noises and squeaks when using the equipment. While sharp noises and squeaks are an indication of stress on the equipment, they can also be hard for an employee to deal with throughout the day. When investing in noise and squeak reduction coatings, you can drastically reduce the noise that is produced.
Ensure Compliance with Warranty and Lender Requirements
Another reason that a company in the auto manufacturing industry should invest in this type of coating is that it can help to protect the equipment warranty and comply with lender requirements. Heavy equipment is very expensive and valuable and many businesses will take out a loan when acquiring it. Depending on the lender, following specific maintenance and protection services could be a requirement. In some cases, this can include having an industrial coating applied. If you have received any type of warranty, it may also require you to have this type of coating.
Improved Efficiency
Margins on vehicle sales and prices can be slim, and cutting costs is very important. One of the ways you can do this is by investing in industrial coatings for your equipment. Not only can this prevent damage and wear and tear, but it will also help ensure the equipment remains efficient. Over the years, this will allow you to produce more cars at a lower cost. This can save you money and boost the bottom line.
Anyone who is in the automotive manufacturing industry is likely very aware of how important it is to keep their equipment in good working order. One of the ways that you can protect your equipment is by investing in quality industrial coating services. When you want to learn more about industrial coating and how it can serve your manufacturing business, you should call us. We can answer all of your questions and help ensure your equipment is appropriately protected.
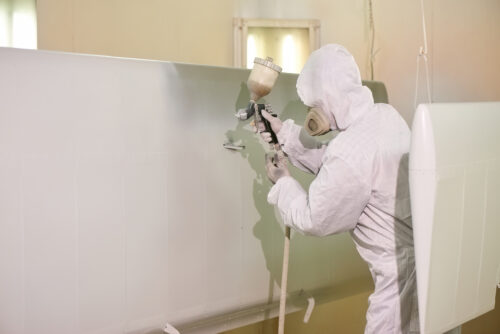
The aerospace industry relies on advanced materials and coatings to achieve optimal performance under extreme conditions. From jet engine components to airframe structures, coatings play a crucial role in corrosion protection, wear resistance, high-temperature stability, and other critical properties. Here at Sun Coating Company, we can help you apply various types of coatings and learn more about them. Here are some of the ways that industrial coatings enhance aerospace parts and lead to improved safety, efficiency, and reliability.
Protecting Against Corrosion
Aircraft operate in harsh environments filled with moisture, salt spray, and wide temperature swings. This leads to corrosion issues that can degrade performance and require expensive repairs if left unchecked. Protective coatings form a barrier between the underlying metal surfaces and the surrounding atmosphere. Cerakote ceramic coatings excel in corrosion protection with excellent adhesion and resistance to UV exposure, chemicals, and thermal cycling. The inert properties of ceramics prevent oxidation and galvanic corrosion between dissimilar metals.
Fluoropolymer coatings like DuPont Teflon PFA provide non-stick surfaces that resist wetting and chemical attack. The stable molecular structure of PFA makes it ideal for corrosion protection in acidic exhaust environments. Electroless nickel coatings offer corrosion resistance by fully encapsulating base metals in an even layer of nickel-phosphorus alloy. This is preferable over plating for complex geometries. Conversion coatings like anodizing and chromating impart corrosion resistance through the growth of surface oxide layers. However, environmental restrictions limit their use compared to protective polymer and ceramic coatings.
Managing Friction and Wear
Moving parts like bearings, gears, and engine components experience friction and repetitive wear. Over time, this can lead to premature failure. Low friction, wear-resistant coatings provide a smooth glide surface and hardness to resist abrasion. Materials like diamond-like carbon (DLC) and molybdenum disulfide (MoS2) minimize friction through unique molecular structures. Tungsten carbide coatings deter wear through extreme surface hardness up to 3000 HV.
Soft, dry lubricants like graphite and boron nitride lower friction without abrasive effects. Fluoropolymers like PTFE reduce friction through slippery molecular chains that easily shear apart. Hard anodizing grows an abrasion-resistant oxide layer on light alloys. The result of low-friction, wear-resistant coatings is improved mechanical efficiency and longer service life of treated components. This reduces maintenance needs and aircraft downtime.
Withstanding High Temperatures
Jet engines, exhaust systems, and other aerospace equipment endure intense heating. Specialized thermal barrier and abradable coatings allow operation at temperatures over 1000°C. Zirconia-based ceramics insulate turbine blades and vanes against hot gas flows. Abradable seals between fan casings and blade tips ablate at contact points to maintain tight clearances. This prevents dangerous gas leakage while permitting free rotation.
Advanced cobalt and nickel alloys resist high-temp oxidation and fatigue. Combining these materials with insulating ceramics and cermets enables lightweight, high-efficiency engine designs. Thermal spray methods deposit thick coatings of corrosion/heat-resistant alloys onto combustion hardware. Line-of-sight techniques like physical vapor deposition apply thin-film coatings of temperature-stable compounds.
Enhancing Appearances
Aircraft exteriors demand coatings that maintain attractive, glossy finishes over years of service. UV-resistant polyurethane clear coats applied over durable epoxy primers give aluminum and composite structures long-lasting protection. MIL-spec coatings like CARC provide chemical agent resistance with a range of colors for military applications. Specialized topcoats containing anti-erosion additives prevent chipping from sand and rain impact. This preserves the aerodynamic shape and radar-absorbing properties of composite stealth aircraft.
Applying the Optimal Coating Solution
With so many coating options available, it’s essential to select the right material and process for each application. At Sun Coating Company, we offer turnkey industrial coating services for the aerospace sector and other industries. Our expertise includes specialized processes like Cerakote ceramic coating ideal for high-heat engine parts. We also apply release coatings for hot plate welding and non-stick surfaces. With decades of experience, we deliver high-quality coating solutions tailored to your application’s demands. Contact us today to discuss your project requirements.
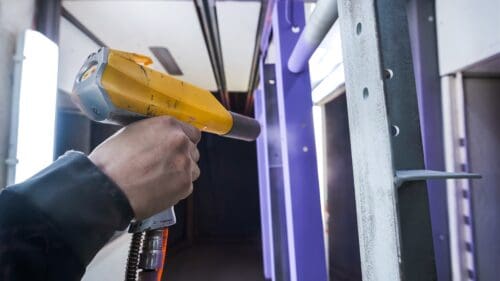
You’ve got so many choices for different coatings now that choosing one can take some time. As you work your way through the number of factors that make a particular coating suitable or not for your equipment, remember to consider whether a liquid or powder coating would be more suitable, too. This may seem like a minor issue, but it can greatly affect your budget and the application process.
The Use of Specialized Equipment to Add the Coating
First, what equipment do you already have for applying the coating, and of the equipment you don’t have, how much are you willing to obtain? Liquid coating application can be as simple as painting with brushes and rollers or maybe a spray gun. If you have to apply liquid coating to much larger parts, you may need additional sprayers that are large enough to handle that job.
Powder coating, though, requires specific applicators to spray the powder onto the surface and then a heat source to heat the part so that the powder melts. If you don’t already have that equipment and don’t have the budget for them, that might make your decision for you regarding liquid vs. powder coatings.
The Shape of the Job
You can dip parts into vats of liquid coating. That makes coating oddly shaped parts much easier. That might not be the case with powder coating, as you have to ensure the powder gets into those harder-to-reach spots.
The Inclusion of Volatile Organic Compounds
A distinct disadvantage of liquid coatings is that the solvents they use can often emit volatile organic compounds, which can be dangerous to breathe in. At best, they can still smell strongly and make people feel ill. Powder coatings like Whitford nonstick coating don’t have these, and they may be a better choice when you’re trying to avoid VOCs. Some liquid coatings and paints may be low-VOC, but that still means there are VOCs present. Some coatings, like Teflon FEP coatings, are available in both liquid and powder form, so the presence of VOCs could be a deciding factor.
The Type of Surface and Its Electrical Conductivity
An issue with powder coatings is that they need electrical conductivity to work. That’s how the powder initially sticks to the part before being melted down. This is used to prevent materials like plastic from being powder-coated. However, now there are electrostatic coatings that you can apply to the surface before adding the powder. So, if you have a material that is not normally conductive, you could still use powder coating, but you’d need to go through an extra step. If you don’t want that extra step, then liquid coating may be more appropriate if other factors align with that decision.
The Ability to Let the Coating Cure
If you’re running a factory that needs to get parts ready and shipped fast, you may want to consider powder coating. Powder often dries and cures faster than liquid coating, especially if you need to apply several coats of liquid coating.
The Budget You Have and the Colors You Want
Two more practical issues to look at are budget, which has already been touched on a bit, as well as the specific color you need. Between the equipment to apply the coating, cure it, and ensure it adheres correctly, will your company be able to obtain everything you need? Powder coating is often more expensive than liquid coating, too.
Do you need a basic color that you can buy off the shelf, or do you need one that has to be specially mixed for your business? Liquid coatings are easier to customize in terms of color; powder coatings are harder to customize and may not be available in large amounts in your customized color.
Sun Coating Company has all the information you need on how liquid and powder coatings compare. Contact us to find out more.
Page 4 of 6« First«...23456»